By Kayla Blackwell | Observer Contributor
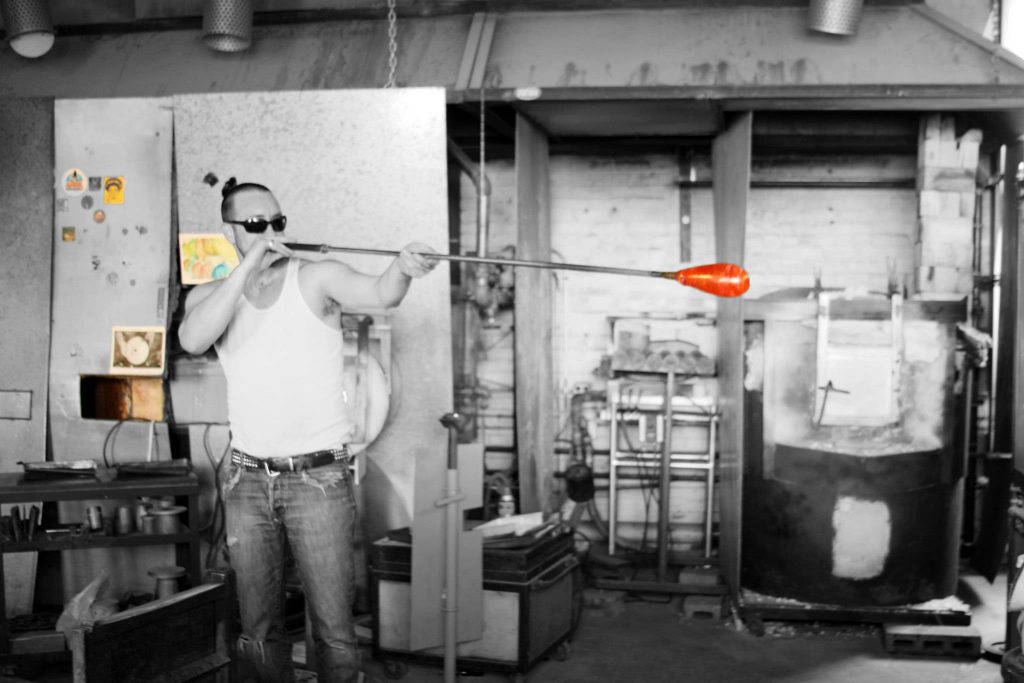
Miles Roache is a student at MWCC who hopes to pursue a career involving glassblowing. Currently in his second year, he plans to earn a business certificate so he can open a shop to sell his work.
Roache began blowing glass in the seventh grade after his father took him to meet a torch worker at an art studio. “I realized this was my passion when I was left alone at the torch to make my own art and realized that my only limits were my imagination,” Roache said.
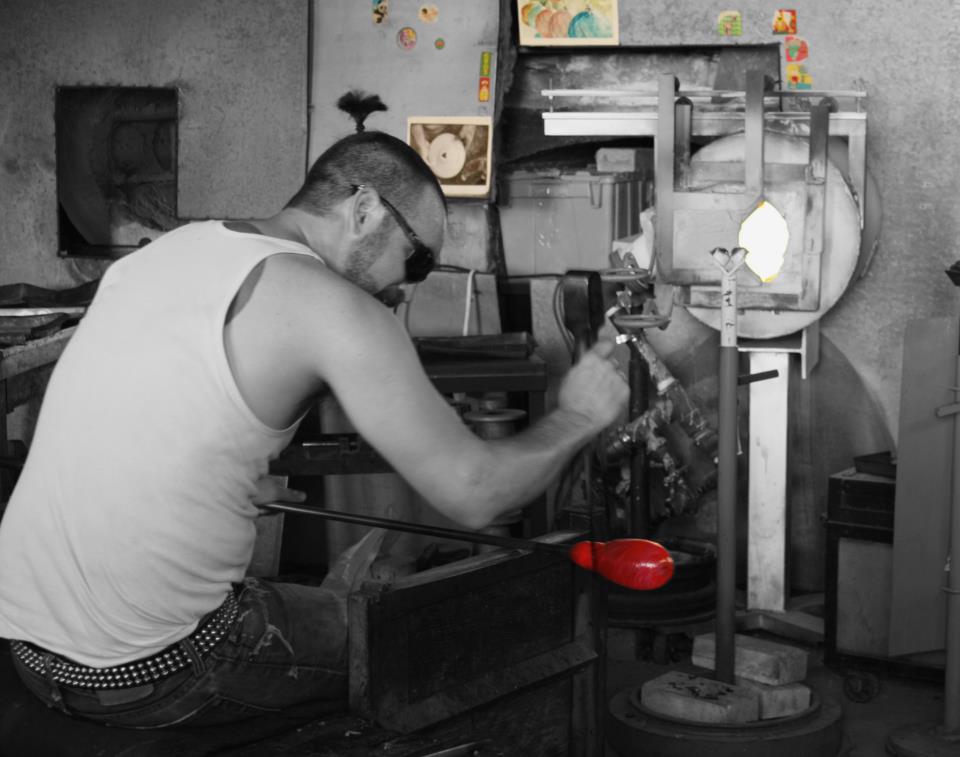
Roache takes classes when he has time in order to strengthen his skills. He has even spent a week in the woods of Western Massachusetts for daily glass-blowing classes. He is currently trying to contact a local glassblower named Kevin Engelmann in order to begin an apprenticeship.
“It’s only difficult to learn if you’re unimaginitive,” said Roache about learning this skill. “You can’t do it if you don’t have steady hands, and you need to be patient.”
Roache said that in order to complete this work, he requires several types of tools, including a table-mounted torch, forceps, tweezers, jacks, and safety glasses. The safety glasses used normally have didymium, which eliminate sodium flares caused from glass hitting the propane torch.
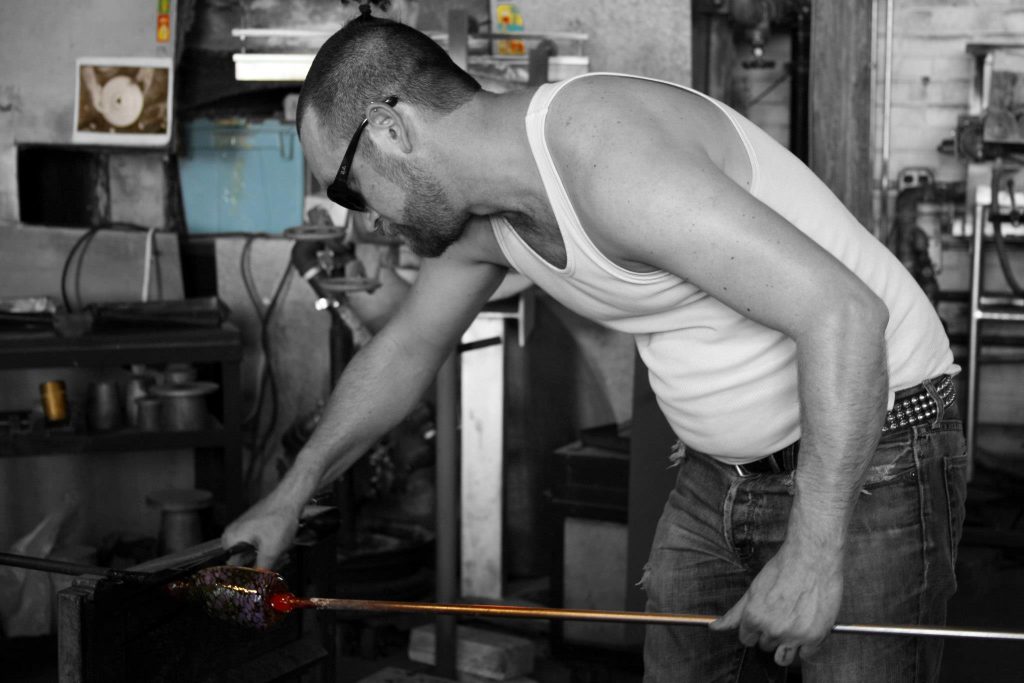
Roache explained that “everything is subject to change when it comes to the process,” but all basic pieces begin with a base gather. A gather is a mound of glass that gets shaped into different parts of the work, such as a leg or a decorative piece, which get attached to each other to form a whole piece. Once all the gathers are shaped and attached to each other, the tweezers and other aforementioned tools are used to further shape it.
Once the piece is completely formed, it gets knocked off the punty (the rod used) and flame polished at its break point so as to avoid having sharp edges or unappealing appearances. Finally, the work is placed in an enealer, which brings the temperature down slowly enough to avoid temperature-shock.
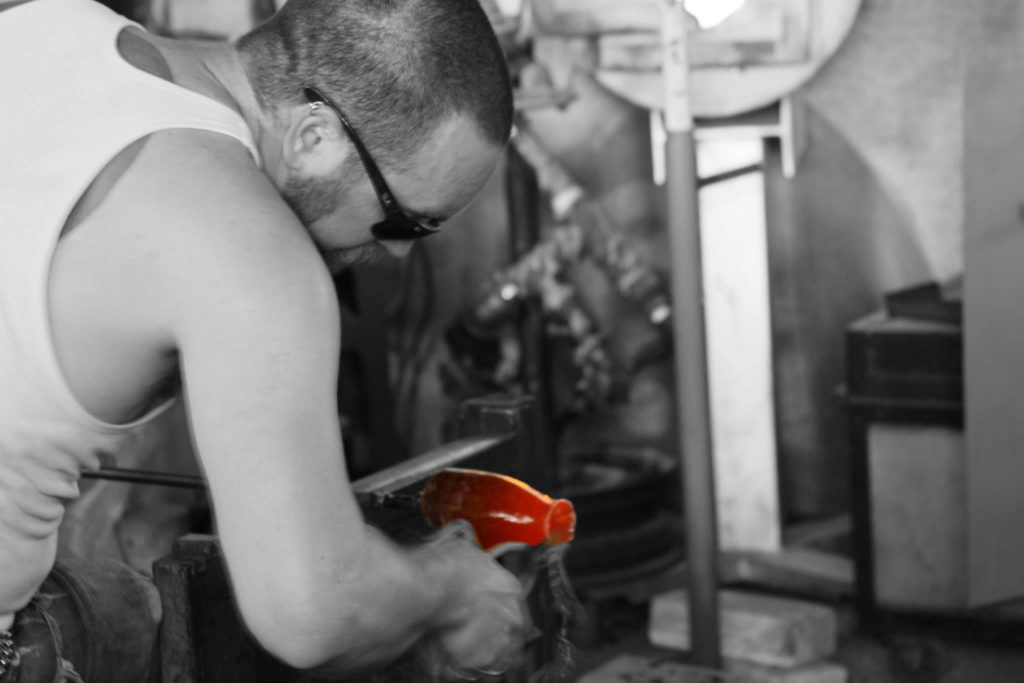
Roache said, “The hardest parts are not burning yourself and working within a small amount of time as to not temperature shock the glass and ruin everything you have just worked on.” Roache’s favorite part of the job is making paperweights because of their abstractness and his freedom to do whatever he wants with them.
In a few years, Roache said he plans to open up an art studio, retail store, and restaurant, “as a fun location where you can watch the glassworking process, purchase various forms of glass art, and grab a delicious bite to eat all at the same time.”
Comments are closed.